Hydraulic Conventional vs Hydraulic MRL: What is the right choice for your building?
by Michael Simmons, DBA, New Installation Sales
As the holidays quickly approach this year, we have more to be thankful for than ever. Soon enough, millions of families across the United States will sit down at the table and engage in healthy conversation. Other than football, perhaps the most common topic of debate will undoubtably be about which hydraulic elevator to use, traditional or machine room-less.
Some may argue with me at this point and suggest that the debate will most likely be traction elevator vs. hydraulic, but I disagree. To prepare for your inevitable holiday debate, this article will compare and contrast traditional hydraulic elevators to the relatively new technology of hydraulic MRL (HMRL).
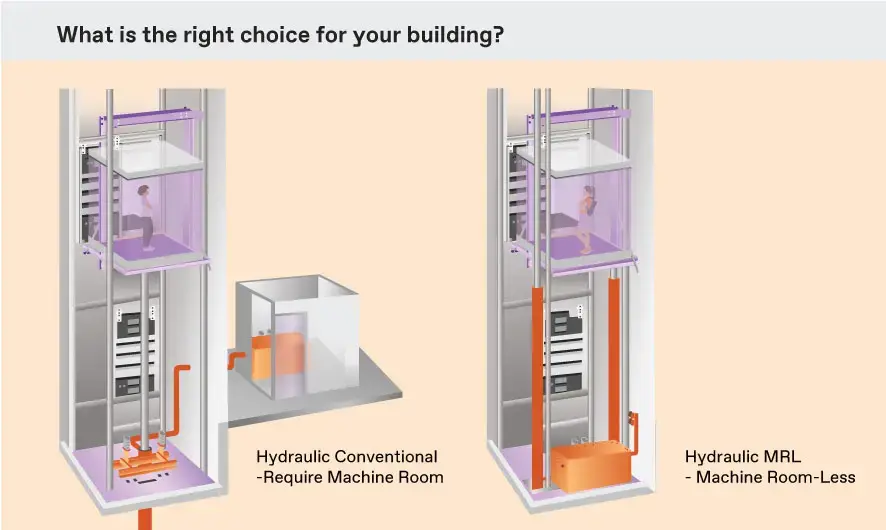
If you’ve ridden an elevator in a two to five-story building, there is a very good chance that it was hydraulic. Instead of relying on a set of cables and pulleys to hoist the elevator from above, a hydraulic elevator relies on an in-ground jack or a set of above-ground jacks to lift the car from below.
Hydraulic elevators are used in low-rise applications because they are more affordable on the front-end (compared with traction) as well as cheaper to service. For decades, hydraulic elevators primarily consisted of an in-ground jack and a power unit located in a nearby machine room. This is known as a traditional hydraulic.
Modern traditional hydraulic elevators may now utilize a set of twin-post, above-ground jacks. In recent years, elevator companies have started to offer a hydraulic elevator with the equipment housed within the elevator shaft; this is known as a Hydraulic MRL, or HMRL. The question now is which one do you choose, traditional or HMRL?
Pros and Cons of Traditional Hydraulic Elevators
The traditional hydraulic elevator does have certain advantages over a Hydraulic MRL. Since the equipment for an HMRL must fit within the elevator shaft, the potential size of the equipment is limited. This puts restrictions on the machine or pump unit for the elevator which in turn limits the weight capacity and speed of the elevator. Since a traditional hydraulic relies on a machine room, if one wants to use a larger machine, simply build a larger machine room.
If you are looking for a high-weight-capacity elevator (such as a service or freight), a traditional hydraulic elevator may be the choice for you.
However, traditional hydraulics that rely on an in-ground jack can be expensive to install due to the need to drill a jack hole as deep as the overall net travel of the elevator. In other words, you will have to dig a hole as deep as the max height of the elevator. That cost can add up.
This also requires coordination of drilling before the building is built and craning in the jack before building the roof. Traditional hydraulics have been around for decades and are reliable and easy to service, but… they require that pesky old machine room.
Pros and Cons of Hydraulic MRL Elevators
The biggest selling factor for an Hydraulic MRL is that it does not require a machine room. This gives the building owner the option to use the space for something other than servicing the elevator, which can be a deciding factor when space is critical.
In retail settings, space = money.
In an HMRL, the power unit and jacks are contained above ground in the shaft, and as such, there’s no need to drill a jack hole. This makes an HMRL the obvious choice for existing buildings that are being renovated or adding an elevator. Since HMRL elevators rely upon twin-post, above-ground jacks, replacing the jacks is much simpler if needed down the road.
There is also no need to run hydraulic pipe from the machine room to the jacks, which removes additional equipment that may be difficult to service or replace.
But HMRL elevators are relatively new technology. As with any newer technology, technical and functional problems may arise until the technology is vetted by time. TKE’s hydraulic MRL technology has been around long enough to flush out and correct issues, but the “newness” has other cons.
In certain jurisdictions, HMRL technology is still not incorporated into elevator code. In Indiana — for example — in order to install an HMRL, the installing company must apply for variance to the elevator code that does not yet recognize HMRL technology.
This adds additional cost for permitting and can be a pain point for elevator inspectors who may differ on their interpretation of what is considered machine space or controller space. Since the equipment is contained in the shaft, some inspectors consider the entire shaft to be “machine space.” This interpretation now changes the lighting and smoke detection requirements in the shaft compared to a traditional hydraulic.
If you have made it to this point of the article, you must really like elevators. More importantly, you have all of the information to hold your own during your holiday debate.
To recap, if you are looking for an elevator to service up to five landings, a hydraulic elevator is most likely your most cost-efficient option. If you are looking for high weight capacity and higher speed options, a traditional hydraulic is the clear choice.
If you are looking for extra space or adding an elevator after a building is already constructed — an HMRL is for you.
Regardless of the outcome of your holiday debate, one thing is clear — if you are looking for an elevator, TKE has the right option for you. To learn more about our state-of-the-art hydraulic applications, take a look at the endura or endura MRL and find what best suits your needs.